Optimization of consumption for constant speed motor applications
Energy savers for fixed speed and variable torque motor applications
7% potential energy savings on average
Electric motors represent a very important part of the electricity consumption. In some processes, the motors are loaded in a sustained and variable manner while running at fixed speed. The installation of an energy optimizer for fixed speed processes makes sense.
The Fixed Torque Process Energy Optimizer is intended for applications where AC asynchronous motors operate at constant speed with or without load variations. This multifunctional controller reduces the energy consumption of motors by up to 25% by adapting the voltage supplied to the motor according to its instantaneous load.
It is installed between the circuit breaker and the equipment motor. The power of the motor gives the size of the optimizer.
Unlike frequency inverters, it does not generate any harmonic pollution in the network. It also improves motor life by reducing hysteresis and eddy current losses in the magnetic circuit, increasing the power factor, and improving the quality of the voltage across the motor, thanks to the input line reactance, which reduces voltage wave distortion.
It offers an interesting alternative to variable speed drives in constant speed applications where the use of a variable frequency drive does not offer any energy saving advantage.
Applications
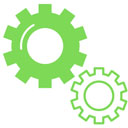
In the industry:
- Conveyors, conveyor belts
- Injection molding machines, extrusion machines
- Air compressors, cold compressors
- Grinders, mixers, etc.
- Pumping
- Elevators,
- Etc.
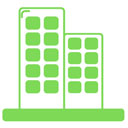
In the building:
- Escalators,
- Elevators
- Fans, Ventilation
- Air conditioning systems, HVAC
- Cold compressors
- Pumps
- Etc.
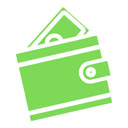
Savings potential with Energy Optimizer
2% – 18%
On engine consumption
We suggest that you do an analysis of your installation for an exact estimate of the savings.
Benefits of our solution
- Reduces engine consumption by 10% to 25%.
- Improves the power factor of the installation
- Reduces iron losses in the motor
- Improves the quality of the voltage supplied to the motor
- Protects the motor and improves its life
- Does not generate harmonic pollution