Optimization of the consumption of variable speed motors
Energy savers for variable torque motor applications
25% potential energy savings on average
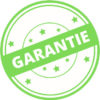
2 YEARS
In some processes, such as pumping, extraction, ventilation or compression, the motors are loaded in a variable way while running at a fixed speed. To regulate the flow rate or pressure of the fluid at the outlet, restriction systems such as valves, vents, etc. are used.
The role of these systems is to increase the pressure drop in the circuit in order to obtain the desired pressure or flow rate. This way of doing things is totally opposed to the idea of saving energy, since it consists in giving full power to the motor and then removing part of the mechanical power obtained at the output, creating losses.
This can be remedied by installing an electronic variable speed drive or variable frequency drive.
This consists of a rectifier (in which the alternating current is rectified), a direct current bus and an inverter which releases a three-phase current at variable frequency. Since the speed of the motor is proportional to the frequency of its power supply, varying the frequency will vary the speed of the motor and therefore the flow rate of the driven pump, fan or compressor.
This technology is only relevant if the operating conditions of the engine fluctuate.
Applications
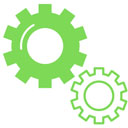
In the industry:
- Pumps
- Fans
- Extractors
- Screw air compressors
- Cold screw compressors
- Shredders
- Mixers
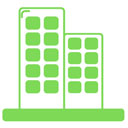
In the building:
- Fans, Ventilation
- Air conditioning systems, HVAC
- Cold compressors
- Pumps
- Etc
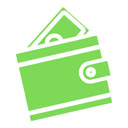
Savings potential with the frequency converter
10 – 40%
On engine consumption
We suggest that you do an analysis of your installation for an exact estimate of the savings
Benefits of our solution
- Reduces engine consumption by 10% to 40%.
- Improves the power factor of the installation
- Protects the motor and improves its life